Empire
Metals Limited / LON: EEE / Sector: Natural Resources
4 September 2024
Empire Metals
Limited
('Empire' or the 'Company')
Positive
Results Achieved from Initial Processing Testwork on Pitfield
Titanium Ore
Empire Metals Limited (LON:
EEE), the AIM-quoted resource exploration
and development company, is pleased to
provide an update on the mineralogical and metallurgical studies
being carried out on titanium rich ores from the
Pitfield Project in Western
Australia ('Pitfield' or the
'Project'). The Company's evaluations to date,
which incorporate both historical research and current
international knowledge and expertise, have identified a number of
highly prospective processing routes which are the focus of
on-going metallurgical testing and flowsheet development. The
testwork is being conducted at a range of independent and
government research laboratory facilities, utilising both
commercial scale equipment and reagent industry vendors. The range
of work programmes is extensive and the understanding being
generated from this breadth of work is integral to the
identification and optimisation of a preferred process flowsheet
and the development of a final product specification for the
Project.
Highlights
· Empire's metallurgical testwork
objective is to develop a processing flowsheet that will enable the
development of a fully integrated, mine to high-value titanium product facility thus achieving our
corporate goal of making Pitfield a globally significant and secure
supplier to the titanium pigment and titanium metal
industries.
· A multifaceted mineralogical and
metallurgical testwork programme has now been expanded, engaging
international and locally based expert consultants, and utilising
Australian based government and commercially owned laboratory
facilities.
· Testwork
conducted to date has been on the fresh bedrock titanite ore.
However, the discovery of concentrated, high-purity anatase in the
overlying weathered bedrock cap has shifted the testwork focus,
requiring the collection of new samples from the diamond drill core
which have now been composited and submitted to the laboratory for
crushing/grinding ahead of mineral concentration testwork.
· Titanite ore testwork has been
focused on separating the Ti-bearing minerals from the low value,
gangue minerals, a key step in the development of an economic
process flowsheet for Pitfield, with positive results achieved
during the initial gravity separation stages on the titanite-rich
fresh bedrock.
·
Preliminary sighter leach tests on titanite ore samples utilising
hydrochloric acid (HCl) have been successful with the contained
titanite mineral grains completely dissolving within 6 hours in an
atmospheric pressure HCl leach at 80 degrees Celsius.
Shaun Bunn, Managing Director, said:
"I am extremely excited by the progress being made
by our development team, led by our Process Development Manager Ms
Narelle Marriott, and well supported technically by titanium
industry specialists, Dr Trevor Nicholson and Mr Eugene Dardengo.
We have commenced research studies with CSIRO and Curtin University
scientists, both groups being located here in Western Australia,
aimed at providing important information on the nature and origin
of the mineralisation as well as the various routes through which
to extract the titanium. Through the mineralogical studies
completed to date at AXT and CSIRO (announced 22 August 2024), we
now have an increasingly detailed understanding of the
mineralisation, both for the fresh and the weathered titanium
minerals, as well as for the gangue minerals.
"We have also been working closely
with titanium industry and market consultants, TiMPC, which are
providing invaluable commercial guidance into what types of
products are most desired by the major titanium industry players
and how Empire can market its high-purity products towards the
high-value end of the market. With new knowledge being generated about
Pitfield's ore geology and the titanium industry market
requirements, plans for the next phase of testwork are being
tailored towards the development of a commercial process flowsheet
optimized for Pitfield anatase and titanite ores."
Mineralogical and
Metallurgical Update
Ore
Characterisation
Two ore types have now been identified within the
host sandstone bedrock at Pitfield: an unweathered or "primary"
titanite-rich ore type present within the fresh sandstone bedrock,
and a weathered or "secondary" anatase-rich ore type present within
the overlying, near-surface cap of weathered sandstone bedrock. The
Company's development team has initially focused on ore
characterisation in order to achieve a fundamental understanding of
the dominant primary and secondary titanium ore minerals (titanite
and anatase respectively), the nature of other associated
titanium-bearing minerals (Fe-Ti Oxides) and the principal gangue
minerals within the near-surface weathered cap (hematite, quartz
and kaolinite). In particular the ores are being characterised by
mineral percentages, the association between minerals, the mineral
grain size and mineral composition including looking for any
impurities.
Several different mineralogical analysis techniques
are being used, including TIMA analysis, XRD, SEM microprobe, and
microscope petrography. These services have been undertaken at
various independent and government owned laboratories including
Automated Mineralogy Incubator (AMI), Bureau Veritas (BV) and
Australia's national science agency, CSIRO.
CSIRO's Geoscience Drill Core Research Laboratory is
unique worldwide, offering a range of multi-disciplinary techniques
for visualising and classifying multi-element geochemical data from
drill holes, core and samples. These highly specialised techniques,
utilising equipment such as the Minalyzer and the HyLogger, will
aid the Company's geoscientists by providing rapid interpretation
of the large data volumes generated from our drilling as well as
generating key geometallurgical characteristics.
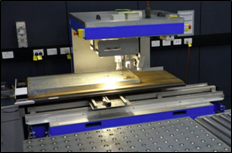
Figures 1-3. (from
clockwise) Narelle Marriott, Empire's Process Development Manager,
reviewing data from the SEM at the AMI laboratory in
Perth.
The HyLogger spectral scanner
and the Minalyzer, both located at
CSIRO's Perth laboratories.
The mineral characterisation studies have included a
wide range of samples from the exploration drilling programmes
completed to date, and include mineralised core samples from the
fresh, transition and weathered zones of bedrock intercepted in the
sampled drill holes; and also multiple large (+80 kg) composite
samples collected from the diamond drill core and crushed and
blended for metallurgical testwork.
These large diamond core composite samples will be
used to test a wide range of mineral processing and
hydrometallurgical techniques. The use of larger composite samples
is important as it allows comparison between processing methods for
testwork undertaken at multiple laboratories.
Once testwork has determined a specific flowsheet as
favourable, then additional samples will be prepared from
historical or new drilling to test ore variability, test flowsheet
variables and to produce bulk samples for engineering and
environmental studies.
Multiple programmes of work are underway, as part of
the metallurgical flowsheet development, discussed in detail below.
The programme has been designed to consider all aspects of a
flowsheet required from delivery of ore to the plant to a final
saleable product to market.
Process Flowsheet
Development
The strategy has been to consider a wide range of
high-potential mineral processing and hydrometallurgical techniques
when designing the on-going testwork programme. The process
flowsheet and related testwork considers four separate, albeit
related, components as defined in Figure 4 below.
The same testwork processes will be used to
separately test the anatase-rich secondary ore and the
titanite-rich primary ore, as the mineral assemblage (inclusive of
the gangue minerals) is entirely different as a result of the
strong, near surface weathering.
Figure 4.
Process Flowsheet components under development
Comminution
Comminution is an initial mineral processing step
aimed at breaking up the mined ore into small enough particles that
the valuable minerals are no longer in the same composite particle
as the gangue minerals. This allows the next step of mineral
concentration to happen more efficiently. Information gained
in the ore characterisation stage has guided the development of
this process flowsheet stage. Mineral grain size and mineral
association are used to determine target particle sizes. The images
from SEM and microprobe work have provided insight into the
physical occurrence of titanium bearing minerals within the
sandstone matrix, thereby focusing the testwork on equipment and
the techniques which can selectively liberate the titanium bearing
minerals without over-grinding, such as mineral sizers, scrubbers,
high pressure grinding rolls, hammer mills and stirred milling.
Standard comminution tests have already been
undertaken on samples from the fresh bedrock and the weathered zone
to provide information on rock competency and energy input for
breakage requirements. The weathered zone was confirmed to be
very soft and the fresh bedrock, whilst more competent, is expected
to fracture easily due to the bedding layers within the sandstone
sediments. Planning is underway for a full range of comminution
tests on both the weathered and fresh rocks, pending receipt of
full diamond 'PQ' drill core.
Mineral
Concentration
Testwork is ongoing at a number of commercial
laboratories for the mineral concentration of the Pitfield primary
ore samples. This programme is testing a wide range of physical and
chemical unit processes that can separate out gangue minerals from
Ti-bearing minerals. Multiple unit processes and combinations that
can be used on the Pitfield ores are being tested to determine how
best to separate the Ti-bearing minerals from the non Ti-bearing
minerals. Additionally the minerals within the non Ti-bearing
stream will be further assessed for their suitability as
potentially economic by-product streams.
As a first stage, screening and size analysis has
been undertaken to investigate the opportunity to produce a
throwaway waste stream within the comminution circuit, with the
objective of reducing the size and energy requirements of the
overall comminution circuit. Some coarse rejection of gangue
minerals was achieved and the suitability of an initial first stage
utilising scrubbing and jigs is now under consideration.
It should be noted that the majority of the testwork
conducted to date has been on composite samples produced from
primary titanite ore. With the discovery of an anatase-rich
secondary ore deposit in the near surface, weathered zone the
testwork focus has shifted to developing an understanding of the
metallurgical characteristics of the minerals within these
weathered secondary ores. This has necessitated further sampling of
the diamond core recovered from the Q1 2024 drill programme. These
samples have now been composited and submitted to the laboratory
for crushing/grinding ahead of mineral concentration testwork.
The key mineral concentration techniques currently
under investigation include:
Gravity separation
testwork is being undertaken at Allied Mineral Laboratories
(AML). AML is an independent mineral processing research facility
located in Perth, Western Australia and specialises in mineral
separation processing testwork and flowsheet design. The initial
gravity tabling tests have been focussed on producing a low-grade
mineral waste stream and a titanium-rich mineral concentrate for
further downstream processing. This research testwork is being
supported by bench scale heavy liquid separation and mineralogical
analysis to determine the optimal separation at different specific
gravities.
Early indications that the primary titanite ore will
respond well to gravity concentration are encouraging. Heavy liquid
separation at a specific gravity cut of 2.9 g/ml rejected 35% of
the mass and 46% of the gangue silicates. Only 10% of the
titanite was rejected in this stream. Further testwork on the
optimal specific gravity cut size and the liberation size to
minimise titanite losses is planned.
Magnetic separation
testwork is being undertaken at both the Bureau Veritas (BV)
mineral laboratory and at Longi, who is a leading manufacturer of
industrial magnetic separation equipment. The research
testwork underway is focused on separating weakly magnetic
minerals, like ilmenite, from non-magnetic minerals such as quartz
or hematite.
Froth Flotation
testwork is being undertaken at both ALS Metallurgy and
Arnofio Flotation Services. Both flotation laboratories bring a
wide range of experience in froth flotation techniques. To date,
the Company has completed over 60 diagnostic flotation tests,
investigating a range of physical conditions and flotation
chemicals.
Figures 5-8
(clockwise from top left) : crushed primary titanite ore prepared
for testwork programmes, Empire Metals' Process Development Manager
observing flotation testwork, close up of a flotation test, gravity
table test in progress and the Longi laboratory scale WHIMS
magnetic separation unit.
Hydrometallurgy
Hydrometallurgical processing, commonly referred to
as leaching, is the process whereby the mineral particles are
partially dissolved and the elements of interest are separated from
other impurities present.
A number of different approaches to this stage of the
process flowsheet have been identified from published research,
standard industrial practice and existing leaching operations.
Bench-scale testwork is determining the leach response of both the
titanium ore minerals and the associated gangue minerals, initially
focused on bringing the titanium into solution, and then looking to
optimise the leach solution chemistry and define the process steps
for product finishing. The testwork is assessing acid types (HCl
and H2SO4) and their consumption, options for
reagent recycling, impurity management and options for producing a
final high-purity titanium product.
Leaching options include a range of temperatures,
under either atmospheric or low pressure leaching conditions.
Previous research on leaching titanite ores indicated that either
sulphuric or hydrochloric acid can be effective. Preliminary
sighter leach tests on Pitfield primary titanite ore samples have
now been completed with positive results. Titanite was shown to
completely dissolve within 6 hours in a concentrated HCl leach at
80 degrees C. Further testwork will be undertaken on the mineral
concentrates generated from the gravity and/or flotation testwork
programmes.
The quality of the concentrates produced in the
mineral separation/concentration step will affect the performance
of the subsequent leaching step. As such, both testwork programmes
will require a feedback loop so that there is the opportunity to
optimise the mineral concentrate quality in order to improve the
outcomes of the titanium extraction step.
Product
Finishing
A high-grade, high-purity titanium dioxide product
suitable as feedstock for chloride pigment production or conversion
into titanium metal sponge, has been identified as the most
desirable final product for the project. The possible process
chemistries in the leaching step provide a good synergy with this
type of final product. The potential optionality to produce a range
of different products, depending on market demand, will be
investigated in the testwork programme. Additionally, any
opportunity to produce a viable by-product and to reduce waste
streams is being explored.
Flowsheet
Design
The extensive range of testwork programmes currently
underway form an important screening process which will help shape
the next phase of research testwork. From these results an in-depth
understanding of the ore is being obtained that will guide the next
phases of testwork and consequently the process flowsheet design.
Results so far have shown a high potential for a multi-stage
mineral separation process flowsheet, likely to include both
gravity and flotation unit processes. A further mineral extraction
processing step using hydrometallurgical leaching techniques is
likely to form the back end of the process flowsheet and allow for
production of a high-grade, high-purity titanium dioxide product.
Testwork is well advanced on the primary titanite ore samples and a
parallel testwork programme is now underway on the secondary
anatase ore.
The Pitfield
Project
Located within the Mid-West region of Western
Australia, near the northern wheatbelt town of Three Springs,
Pitfield lies 313km north of Perth and 156km south of Geraldton,
the Mid West region's capital and major port. Western Australia is
ranked as one of the top mining jurisdictions in the world
according to the Fraser Institute's Investment Attractiveness Index
published in 2023, and has mining-friendly policies, stable
government, transparency, and advanced technology expertise.
Pitfield has existing connections to port (both road & rail),
HV power substations, and is nearby to natural gas pipelines as
well as a green energy hydrogen fuel hub, which is under planning
and development (refer Figure 9).
Figure 9. Pitfield Project Location showing the
Mid-West Region
Infrastructure and Services.
Since commencing its maiden drill
campaign in March 2023, the Company has completed a total of 107
drillholes for 17,003m (including seven diamond core holes for
2,025m), of which 67 RC drillholes and six diamond core drillholes
were drilled within the Cosgrove and Thomas prospects (Figure 10).
The drilling shows a high-grade (>5% TiO2), more than
1km wide central core running on a north-south trend through both
mineral prospects, which could join between the two prospects
thereby representing a potential total strike length of more than
20km. Significantly, the RC drillhole results clearly indicate
elevated TiO2 grades are present within the top 40m
(RNS: 15 May 2024).
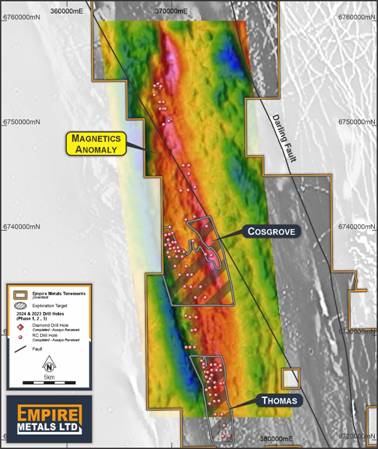
Figure 10. Grey-scale magnetics map overlain
by airborne gravity survey results with the location of RC and
Diamond Core drillholes and the Cosgrove and Thomas Exploration
Target.
Market Abuse Regulation (MAR)
Disclosure
Certain information contained in
this announcement would have been deemed inside information for the
purposes of Article 7 of Regulation (EU) No 596/2014, as
incorporated into UK law by the European Union (Withdrawal) Act
2018, until the release of this announcement.
**ENDS**
For further information please visit www.empiremetals.co.uk or
contact:
Empire Metals Ltd
Shaun Bunn / Greg Kuenzel /
Arabella Burwell
|
Tel: 020 4583 1440
|
S. P. Angel Corporate Finance LLP (Nomad &
Broker)
Ewan Leggat / Adam Cowl
|
Tel: 020 3470 0470
|
Shard Capital Partners LLP (Joint
Broker)
Damon Heath
|
Tel: 020 7186 9950
|
St Brides
Partners Ltd (Financial
PR)
Susie
Geliher / Charlotte Page
|
Tel: 020
7236 1177
|
About Empire Metals
Limited
Empire Metals is an AIM-listed
exploration and resource development company (LON: EEE) with a
primary focus on developing Pitfield, an emerging giant titanium
project in Western Australia.
Exploration activity at Pitfield has
confirmed the discovery of a new giant mineralised system extending
over 40km by 8km by 5km deep. Drilling campaigns have confirmed
high-grade TiO₂ mineralised zones across thick bedded intervals to
a vertical depth of ~350m, confirming Pitfield as a world class,
district-scale titanium mineral system.
Empire is now accelerating the
economic development of Pitfield, with the objective of becoming a
leading producer of high value titanium dioxide
products.
The Company also has two further
exploration projects in Australia; the Eclipse Project and the
Walton Project in Western Australia, in addition to three precious
metals projects located in a historically high-grade gold producing
region of Austria.